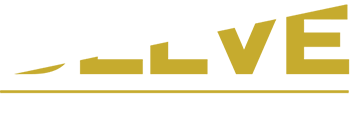
Specialist in Underground Mining Optimisation.
There are three well known aspects of creating a drill & blast design. It is crucial to consider how each hole will be fired – engineers will take into account the void, break-out angle and firing sequence. However, there is a fourth dimension that must be considered in order to optimise a stope’s output: time.
Most mine sites have drill & blast guidelines, which state what the burden & spacing used on site are. These rules ensure that designs are created to the same standard but can also lead to little thought about how each hole will fire.
Too often, drill & blast design is approached as a three-dimensional task completed on a two-dimensional screen, and this vitally important fourth dimension is forgotten.
When timing is considered during the design phase, key factors can be optimised; for example the amount of free bog (draw point material), which would improve extraction of the ore or the direction of throw to increase recovery. The timing of a blast will also affect the fragmentation of the fired material, which has a major influence on the material’s bogging, trucking & crushing.
The below images hows the relation between timing and fragmentation*, with an optimum suggested delay of 5 to 25ms per hole. A benefit of achieving a finer fragmentation is the increase throughput of a mill, if optimised to do so.
Stope blasting is the first process in which comminution takes place. It is also the cheapest process in which to achieve the best results; reducing the mill feed size reduces the requirement for crushing, a common bottleneck. It is always worth a mine investing in its drill and blast designs to ensure that the entire site continues to run smoothly and to its highest capacity.
To conclude, when creating a drill & blast design the thought process behind each hole and how it will be fired can have an effect much further than just a successful blast & reconciliation. Delve Mining Solutions can fill gaps in the knowledge of onsite engineers through training or by providing up-to-date blasting guidelines to a site. Furthermore, by hiring a short-term DMS Engineer to complete the drill& blast designs for immediate success, sites will ease the pressure felt by onsite engineers. This will allow them to attend to the critical QA/QC activities often left unattended when a site is understaffed.
*(2007 Institute of Materials, Minerals and Mining – Design methodology for underground ring blasting I. Onederra & G. Chitombo)